Fluorine chemical industry, known as the "gold industry" in fine chemicals, has long been monopolized by foreign countries in the synthesis technology of hydrofluoroether and perfluoropolyether, and the product prices are high, which has become a "bottleneck" problem restricting the development of China's fluorine chemical industry.
As a subsidiary of a large state-owned enterprise, Company T mainly engages in the production and manufacturing of chemical materials. To achieve the domestic substitution of high-grade fluorine chemical materials, it has initiated technological research and development in the synthesis technology of hydrofluoroether and perfluoropolyether, which is more energy-efficient, environmentally friendly, safe and effective.
As one of the national key projects, Company T has encountered various "challenges" during its exploration of large-scale production. Among them, the production line of the hexafluoropropylene oxide project has faced a temperature control problem.
High failure rate and high energy consumption? Afraid of downtime?
Part 1 Industry Pain Points

In the field of new chemical materials, especially in the fluorine chemical industry within the semiconductor chemical sector, the production process has extremely strict requirements for the precision, stability and energy efficiency of temperature control equipment.
Before introducing the high-end equipment from Suzhou Aode, the customer had been using decentralized individual temperature control devices (such as single chillers and mold temperature control units) for heating and cooling during the production process. Drawbacks keep emerging during the usage process:
High cost | The equipment is large in size, has a high purchase cost and high energy consumption
High failure & downtime risk | High failure rate, frequent shutdowns for maintenance
The operation is cumbersome | Starting and stopping are troublesome (especially when restarting after stopping)
Insufficient temperature control accuracy | may affect product quality and consistency
More importantly, frequent equipment malfunctions and shutdowns for maintenance not only disrupt the production rhythm but also the complex process of restarting the equipment may affect product quality, leading to a significant increase in production costs. To achieve continuous production, precise temperature control of the equipment and energy-saving effects, Company T urgently needs to find new solutions.
After consulting multiple companies, T Company chose Aode because it can meet the temperature control requirements of the entire refrigeration and heating range and has a wealth of industry cases.
How does Aode's "non-standard Customization" solve the pain of downtime?
Part 2 Solution
In response to the high requirements of T Company for the stability, accuracy and continuity of temperature control in its production process, Suzhou Aode High-end Equipment, with its profound industry experience and innovative technology, has tailored a centralized temperature control solution for it, helping the customer achieve efficient, reliable and low-cost continuous production and accelerating the process of import substitution.
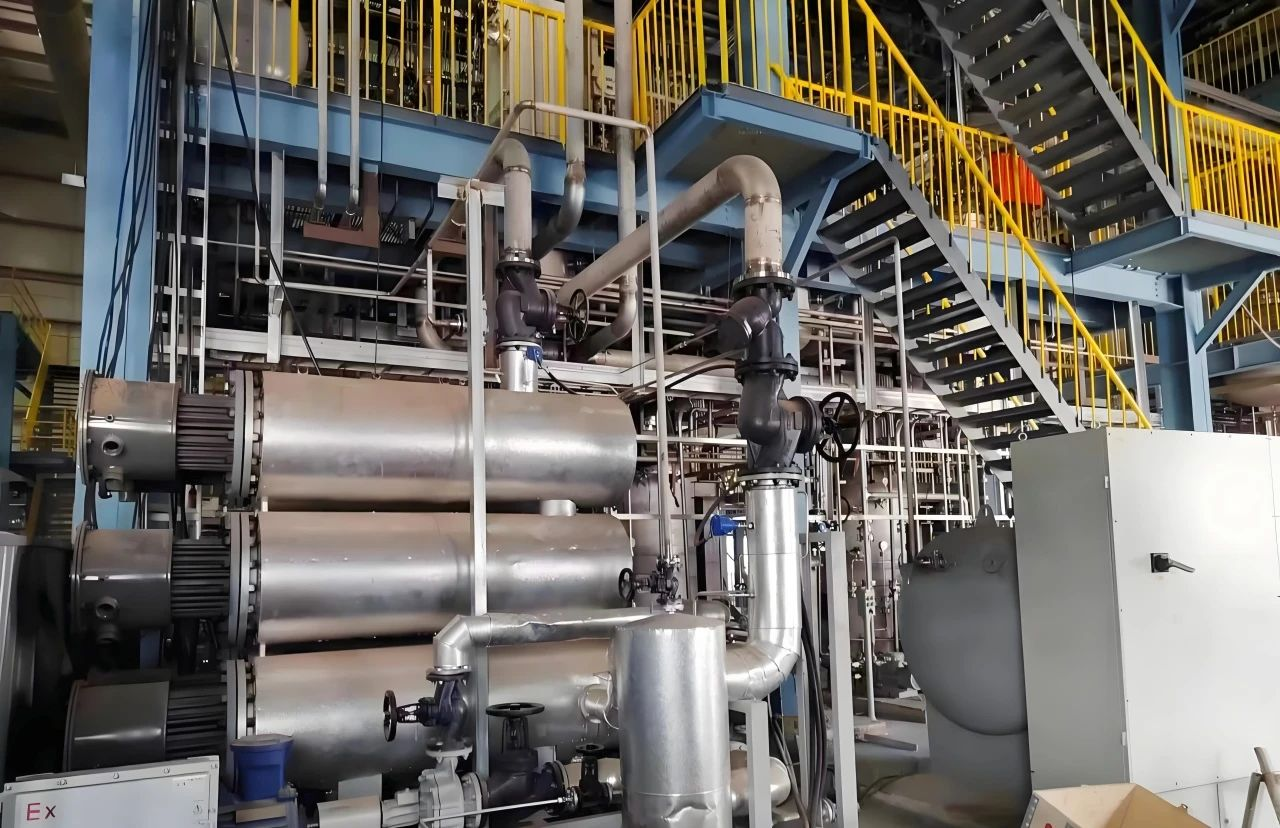
Aode centralized temperature control solution
A centralized control system is adopted to uniformly manage 29 temperature control devices (chillers, storage tank units, refrigeration TCUs, 720KW organic heat carrier furnaces, and three-in-one oil temperature control machines).
/////////////////
According to the temperature requirements of different process links, Aode rationally arranges various types of equipment at different positions to achieve customized temperature control services, in order to achieve the goals of precise temperature control, energy conservation, convenient use and risk avoidance.
The TCU equipment allocates heat according to different process requirements. The organic heat carrier furnace provides thermal energy for the entire workshop. The multi-machine integrated oil temperature control machine precisely controls the temperature of each reaction vessel's temperature zone, while the low-temperature chiller is responsible for cooling the system. The cooling temperature can reach -50 ℃ and the heating temperature can reach 180 ℃, meeting the temperature control requirements of a single temperature zone.
It is worth mentioning that the cascade temperature control for controlling the gas phase temperature is the key technical breakthrough of this scheme. By controlling the temperature of the storage tank unit (serving as an "intermediate buffer/stabilization source") through multiple machines and then precisely distributing it to the downstream TCU, high-precision and stable control of the gas phase temperature is achieved.
This is crucial for chemical reaction processes (such as the production of hexafluoropropylene oxide), and it is also applicable to customers who do not want to shut down, are worried about equipment failure, and want to save energy.
The transformation from "frequent shutdowns" to "continuous and efficient operation"
Part 3 Implementation Effect
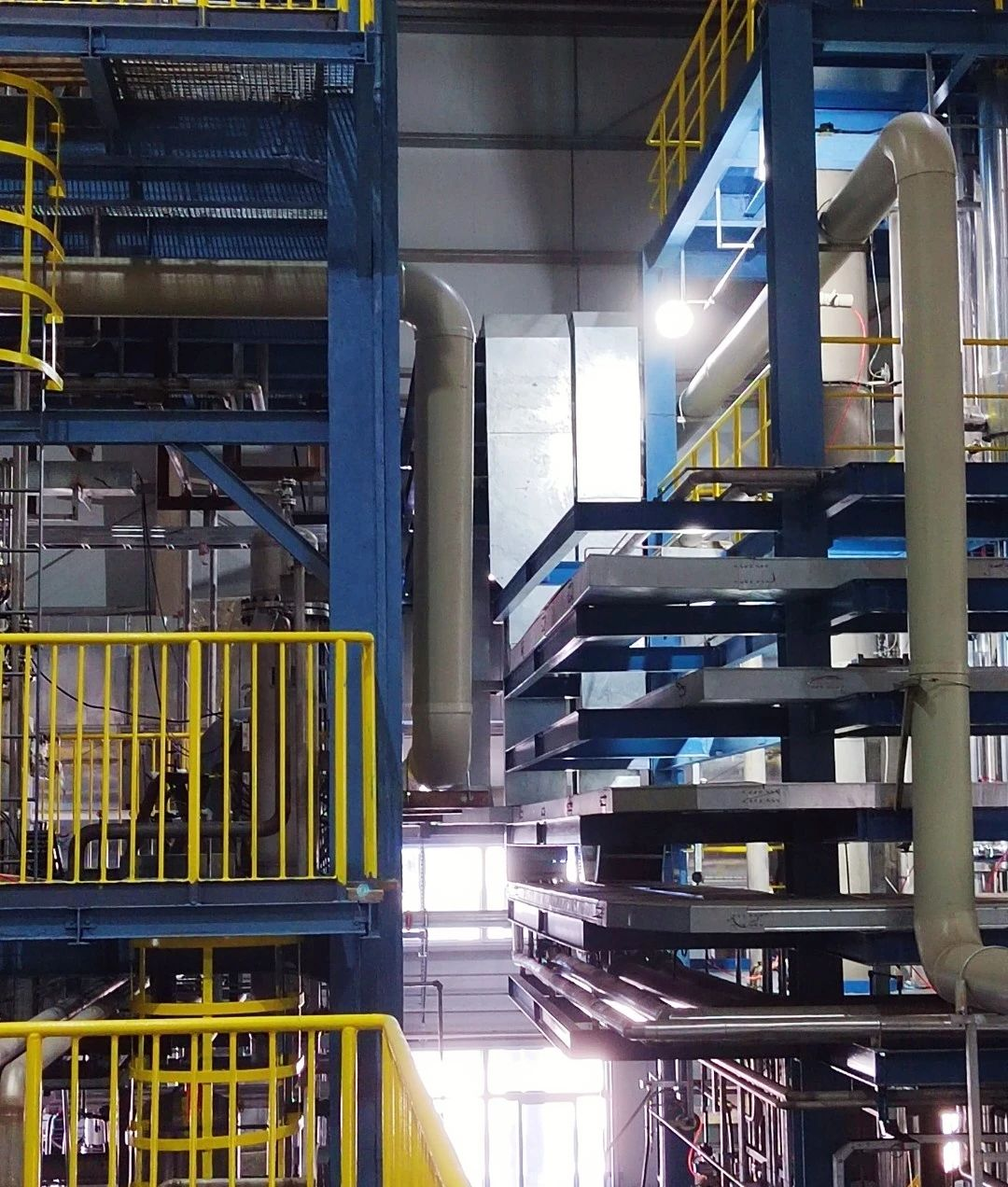
Aode centralized temperature control solution
Through the Aode temperature control solution, T Company has achieved an all-round improvement:
Multi-machine backup for key links (cold source, heat source), automatic seamless switching/isolation in case of single-machine failure, ensuring stable energy supply for storage tank units, significantly reducing the risk of total production halt, and meeting customers' extreme requirements for production continuity.
Centralized energy supply has high efficiency. Compared with decentralized single machines, centralized cooling/heating significantly improves the overall energy efficiency of the system. At the same time, it covers a wide temperature range from -50℃ to 180℃, meeting complex process requirements in one stop. It is also convenient for flexible expansion in the future according to changes in production capacity or processes.

Your production line is just one step away from "high efficiency and energy conservation"!
The requirement for production continuity is extremely high
It is hoped to reduce energy consumption, maintenance costs and the hidden costs caused by equipment failures
Stable and precise temperature control and optimized layout are required
Aode has been dedicated to high-end industrial temperature control for 21 years, focusing on the research and development, production and sales of precision industrial temperature control equipment. It is committed to providing customers with efficient, safe and environmentally friendly industrial temperature control system solutions. Aode has always adhered to a diversified business strategy and possesses a comprehensive product system covering heating, cooling and integrated cold and heat. We can provide one-stop, diversified and customized temperature control system solutions for different industries.
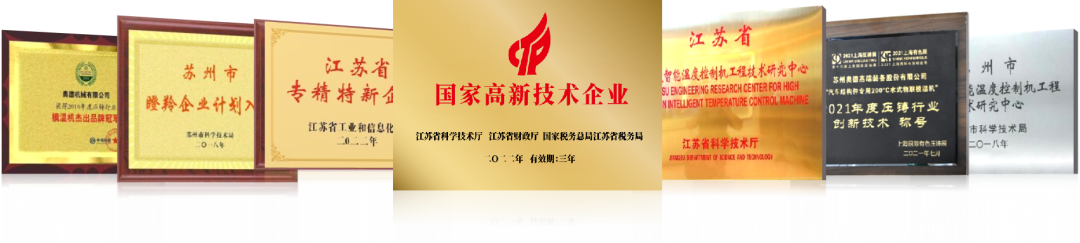
